So having recently come from a night freight operation where we were quite often operating towards the limits of the Maximum Flight Duty Period (MaxFDP) – After having stuffed up the calculations a couple of times, I decided to create a VA Max FDP Calculator Spreadsheet that would calculate for me the number I usually […]
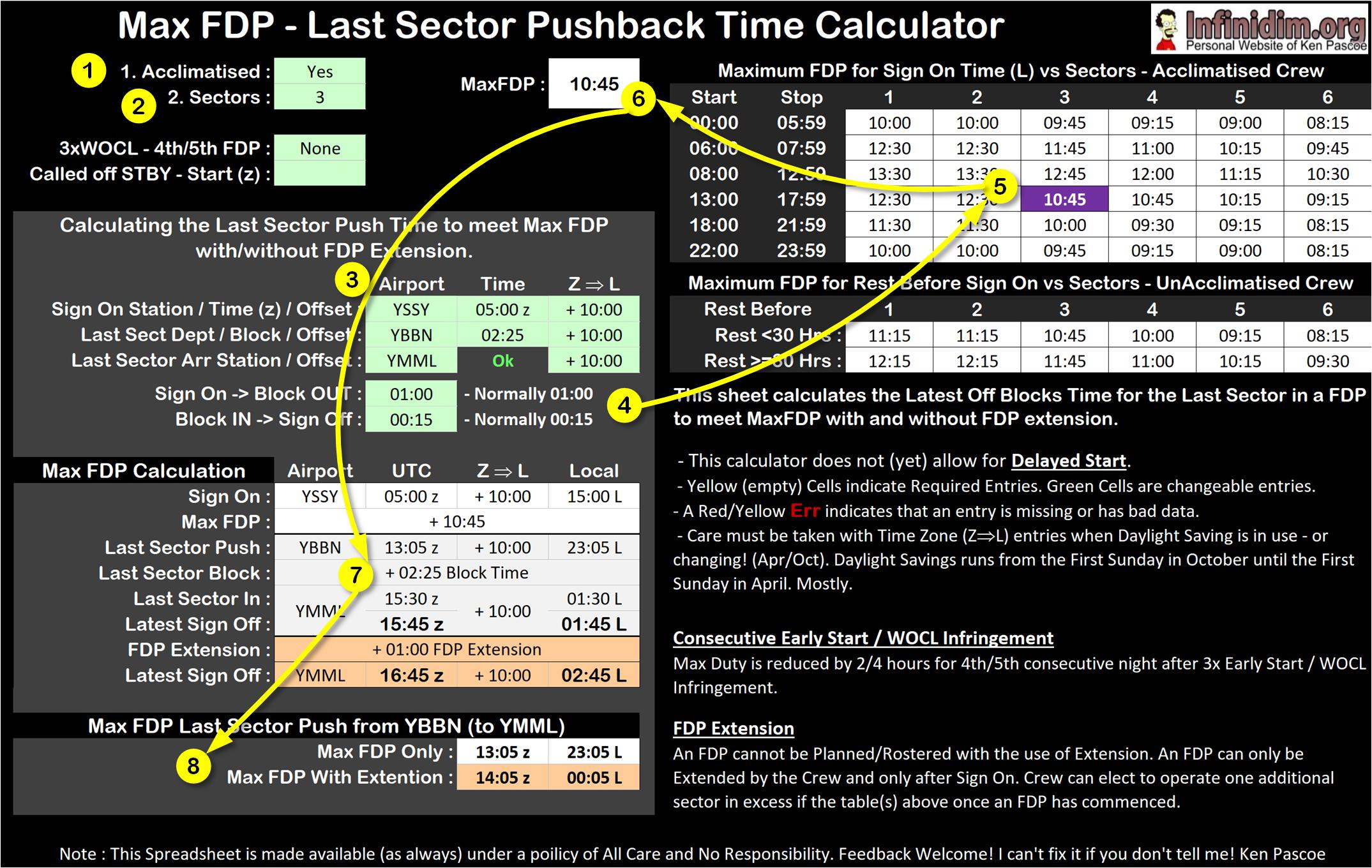